在自动化生产线或精密装配环节,机器手能否高效、可靠地完成任务,末端执行器——夹爪的选择至关重要。选型不当,轻则影响生产效率,重则导致设备损坏、产品报废。面对市场上琳琅满目的夹爪产品,从业者往往困惑:究竟如何才能选出最适配应用需求的夹爪? 本文将聚焦两个最基础也最关键的考量维度——负载重量和操作精度,为您提供清晰的选型思路。
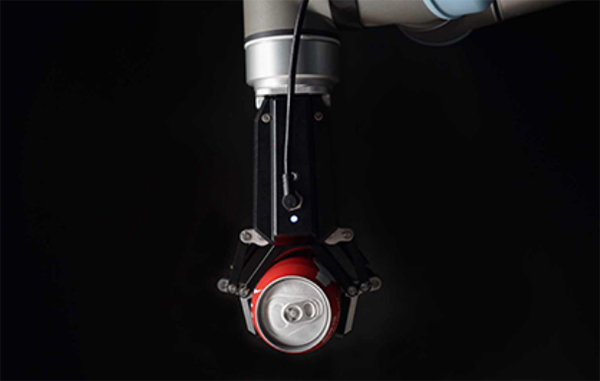
一、 夹爪选择:自动化应用的成败关键
机器手夹爪如同人类的手,是实现与工件交互、完成抓取、搬运、装配等动作的直接执行部件。其性能的优劣直接决定了整个自动化单元的效率和可靠性。一个不匹配的夹爪,可能会成为自动化改造的“阿喀琉斯之踵”,导致投资难以获得预期回报。因此,在规划自动化方案之初,准确评估和选择夹爪是必不可少的一环。
负载重量和操作精度是夹爪选型过程中不可回避、且必须优先厘清的核心指标。它们是夹爪能否胜任工作的基石。
二、 负载重量:夹爪的承载之本
负载重量并非仅指被抓取工件的静态重量。 它包含两个关键部分:
1.工件自重:即夹爪需要抓取的物体本身的重量。
2.动态力:机器手在运动过程中产生的附加力。具体包括:
加速度力:机器手启动或加速时,由于惯性作用施加在工件上的额外力(根据牛顿第二定律 F = m a)。
减速度力:机器手停止或减速时产生的惯性力。
离心力:机器手进行旋转运动时产生的向外的作用力。
外部作用力:如在装配过程中遇到的阻力、振动等。
选型依据:预留安全空间
必须选择额定负载大于实际最大负载的夹爪。 这是铁律。额定负载是制造商在特定条件下(如夹持点位置、速度)保证夹爪能安全可靠工作的最大负载值。
务必考虑安全系数。 由于实际工况复杂多变(如冲击、振动、摩擦变化),建议在选择额定负载时,将计算得出的最大实际负载(工件自重 + 最大动态力)乘以一个安全系数(通常为1.5至2倍)。例如,如果最大计算负载为10公斤,则应选择额定负载至少为15公斤至20公斤的夹爪。
负载不足的严重后果
夹爪损坏:长期超负荷工作必然加速夹爪内部结构(如齿轮、连杆、气缸/电机)的疲劳和磨损,导致过早失效甚至断裂。
精度下降:负载过重会使夹爪爪指变形、驱动机构打滑,造成抓取位置偏移、晃动,重复定位精度丧失。
寿命急剧缩短:持续的过载运行是夹爪寿命的头号杀手。
应用失败:根本无法稳定抓取或搬运工件,自动化流程中断。
三、 操作精度:夹爪的掌控之魂
操作精度决定了夹爪能否精细、稳定地完成预定动作,尤其在精密装配、微小零件处理等领域至关重要。它包含几个相互关联的维度:
1.重复定位精度:夹爪爪指多次开合到同一指令位置的一致性误差(通常以±毫米或微米表示)。例如,指令张开到50mm位置,每次实际到达的位置在49.98mm至50.02mm之间波动,则其重复定位精度为±0.02mm。
2.抓取精度:夹爪在抓取工件时,爪指实际接触点相对于期望接触点的位置偏差。这直接影响工件在夹爪中的初始定位。
3.力度控制精度:夹爪实际施加在工件上的夹持力与设定目标夹持力之间的误差。这对于易碎、易变形工件(如玻璃、薄壁件、精密电子元件)的保护至关重要。
选型依据:匹配精度需求
明确应用精度门槛:不同应用对精度要求差异巨大。普通搬运(毫米级)?精密组装(亚毫米级)?半导体或生物医疗(微米级甚至更高)?必须首先界定所需精度级别。
精度驱动类型选择:
电动夹爪:通常具备更高的重复定位精度(可达±0.01mm甚至更高)和优异的力度控制精度(可精确到零点几牛顿)。因其采用伺服电机和闭环控制,编程灵活,适合高精密装配、实验室自动化、电子组装等场景。
气动夹爪:通用性强,成本较低,速度快。但重复定位精度(通常在±0.1mm左右)和力度控制精度相对较低(通过调压阀控制,精度受气源波动影响)。适用于精度要求不高、需要快速开合的搬运、码垛等场合。
关注结构刚度与驱动控制:夹爪本体和爪指的结构刚性直接影响其抵抗变形、保持精度的能力。驱动方式(电机/气缸)和控制算法(开环/闭环,力控策略)是精度实现的底层保障。
精度不足的连锁反应
装配失败:零件无法精确对位,插针插不进孔,螺丝拧不正。
产品损坏:力度过大压碎玻璃、压伤产品表面;力度过小导致工件在运动中掉落。
过程不稳定:良率波动大,需要人工频繁干预调整,丧失自动化意义。
效率低下:频繁的失败和重新尝试拖慢整体生产节拍。
四、 其他考量点
在确保负载和精度满足核心需求后,还需综合评估以下因素,使选型更完善:
1.工作环境适应性:
洁净度要求:半导体、医药行业需要无尘室等级的夹爪,防止产生颗粒污染。夹爪材质和润滑需特殊设计(如采用不锈钢、真空兼容润滑脂)。
油污/粉尘环境:如铸造、机加工车间,夹爪需要良好的防护等级(IP65/IP67以上),防止油污侵入导致故障或精度丧失。
高温/低温:特殊环境(如热处理、冷库)要求夹爪材质和内部元件(密封件、传感器、润滑脂)能耐受极端温度。
腐蚀性环境:化工、食品加工等场合需耐腐蚀材质(如不锈钢、特定涂层)。
2.夹持方式匹配:
外夹:最通用,从外部夹持工件。
内撑:适用于有内孔或内腔的工件(如轴承套圈、瓶罐)。
吸附:利用真空(吸盘)或磁力吸取平面、光滑或铁磁性工件。需考虑工件表面特性、透气性。
根据工件形状、抓取点位置和工艺要求(如是否需接触特定表面)选择最合适的夹持方式。
3.通讯接口兼容性:
夹爪需要与机器手控制器顺畅通讯,接收指令并反馈状态(如开合到位、夹持力值、故障信息)。
确保夹爪支持的通讯协议(如IO、Modbus TCP/IP、EtherCAT、Profinet、EtherNet/IP)与您的机器人系统兼容。集成难度和成本需提前评估。
五、 精准选型:始于需求,终于匹配
选择机器手夹爪,绝非简单地对比规格参数表。负载重量(含动态力)和操作精度(定位、抓取、力度)是选型成功的两大基石。 它们是衡量夹爪是否能“拿得动”且“拿得稳”、“拿得准”的核心标尺。
精准匹配需求是成功的关键:
1.深度剖析应用:详尽列出工件的重量、尺寸、形状、材质、表面特性;精确分析机器手的运动轨迹、速度、加速度;明确环境条件和对精度的硬性要求。
2.精研规格参数:仔细查阅供应商提供的详细产品规格书,重点关注额定负载(含适用的夹持点)、重复定位精度、力度控制范围与精度、结构尺寸、防护等级、温度范围、通讯接口等关键指标。切勿只看最大开合行程等基本参数。
3.善用专业支持:对于复杂或关键应用,积极与夹爪供应商或系统集成商的技术专家沟通,获取专业的选型建议和应用验证。他们拥有丰富的行业经验,能规避潜在风险。
选择正确的夹爪,是释放机器手全部潜能、构建高效可靠自动化单元不可或缺的第一步。锚定负载与精度,系统评估,精准匹配,方能奠定自动化成功的坚实根基。
六、机器手夹爪推荐
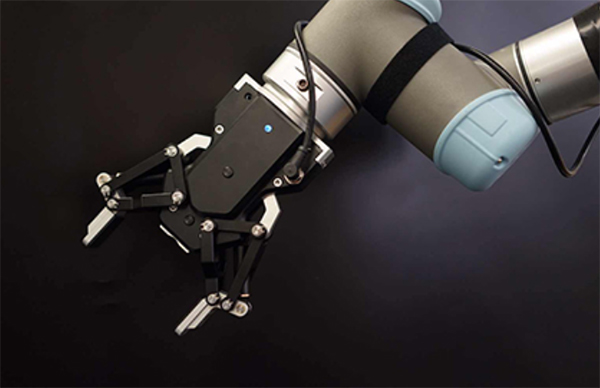
大寰AG 系列关节型自适应电爪,适用于协作机器人,以精巧的结构设计适配对不同形状工件的稳定抓取。以优异的产品设计,AG系列分别荣获2019年和2020年红点设计奖。夹爪连杆机构支持包络自适应抓取,更适应圆形、球形或异形物体,提高抓取稳定性。
总结:
选择机器手夹爪的核心在于精准匹配需求,负载重量(含动态力)与操作精度(定位、抓取、力度)是两大决定性因素。透彻分析应用场景,精研产品规格,必要时借助专业支持,确保夹爪在承载能力、精细操作上完美契合任务要求,是自动化应用高效、稳定、可靠运行的根本保障。